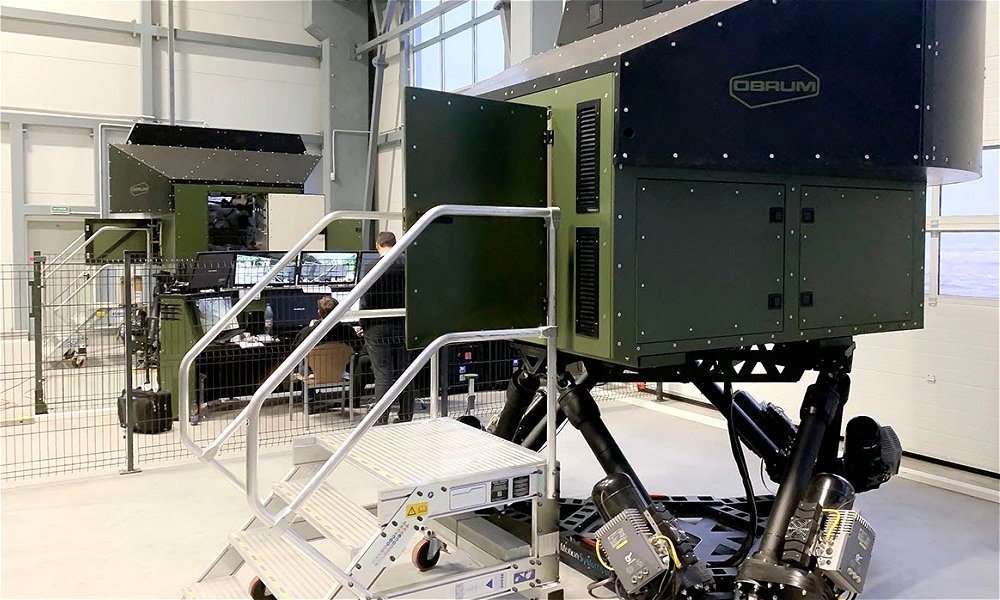
Types Of Motion Simulators
Hydraulic vs. Electric Systems
Motion simulators have revolutionized entertainment, training, and gaming experiences, offering immersive adventures that push the boundaries of reality. At the heart of these simulators lie two primary systems: hydraulic and electric. Each system comes with its own set of features, advantages, and limitations, catering to diverse applications and preferences. In this blog, we'll delve into the differences between hydraulic and electric motion simulators, exploring their mechanics, performance, and suitability for various purposes.
Electric Motion Simulators:
Electric motion simulators utilize electric motors, drives and a controller, to generate motion cues. These systems rely on precision control algorithms to translate digital data into physical movement. Here's a closer look at their characteristics:
Precision Control:
Electric motion simulators offer a more precise control over hydraulic systems simulating parameters such as acceleration, velocity, and position. This level of control allows for accurate replication of various motion profiles, enhancing the realism of the simulation. Typically, a controller receives a command from the host computer which then sends out a +/- signal to the electric drives, which converts that signal to an output to the motors.Low Maintenance:
Compared to hydraulic systems, electric motion simulators typically require less maintenance. Electric motors have fewer moving parts, reducing the likelihood of mechanical failures and the need for hydraulic fluid changes.Energy Efficiency:
Electric motion simulators are generally more energy-efficient than hydraulic systems. They consume power only when in operation, leading to lower overall energy consumption and operating costs.Compact Design:
Electric motion simulators often have a more compact design compared to their hydraulic counterparts. This makes them suitable for applications where space is limited, such as home sim racing setups or compact training facilities.
Hydraulic Motion Simulators:
Hydraulic motion simulators require hydraulic actuators, a hydraulic pump, manifold, and servo valves, to generate motion cues. These systems rely on pressurized hydraulic fluid to move the simulator platform. Here are some key characteristics of hydraulic motion simulators:
High Payload Capacity:
Hydraulic systems are capable of handling higher payload capacities compared to electric systems. This makes them suitable for simulators that require the ability to support heavier loads, such as flight simulators or heavy equipment training simulators.High Fidelity Motion:
Hydraulic motion simulators are known for their high-fidelity motion cues. The use of hydraulic actuators allows for rapid and forceful movements, providing a more immersive experience, especially in scenarios requiring intense motion, such as racing or flight simulations.Fluid Leakage Concerns:
One of the main drawbacks of hydraulic motion simulators is the potential for hydraulic fluid leakage. This can lead to maintenance challenges and environmental concerns, especially in applications where spills can cause damage or contamination. However, hydraulic seals have improved over the years making leaks even more uncommon.Higher Maintenance Requirements:
Hydraulic systems typically require more maintenance compared to electric systems. Regular checks and maintenance of hydraulic fluid levels, seals, filters, and hoses are necessary to ensure optimal performance and prevent potential issues.
Conclusion:
Both electric and hydraulic motion simulators offer unique advantages and disadvantages, making them suitable for different applications depending on specific requirements and preferences. Electric systems excel in precision control, energy efficiency, and low maintenance, while hydraulic systems offer high payload capacity, high-fidelity motion, and robustness. Understanding the differences between these systems is crucial for choosing the right motion simulator for your needs, whether it's for entertainment, training, or research purposes.